Chillers for Plant Extracts
LNEYA has been the temperature control experts, We work directly with the scientist and engineers developing the processing technology. These developments have yielded the most efficient and reliable temperature control equipment in the industry. Our efficiency is achieved through utilizing a combination of variable speed technology and adaptive control logic. Our reliability is achieved through robust component selection and quality production control.

LNEYA can provide temperature control by circulating fluids at -150℃ through 350℃ (-238ºF to 662ºF). These industry specific models take into account the unique requirements of Cannabis processing. In particular, LNEYA Dynamic temperature control systems are easy to install/operate, have the lowest operational costs and have unmatched reliability.
One of the key aspects to successful and efficient Cannabis processing is accurate and reliable temperature control. Temperature control is necessary in both the extraction and distillation processing steps. Whether extraction is achieved through Carbon Dioxide Systems, Liquefied Hydrocarbon Systems or Ethanol Systems, temperature control is at the heart of the process.
The clear choice for Cannabis processing temperature control is LNEYA.

Supporting Cannabis Extraction & Distillation
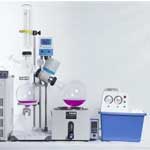
Rotary Evaporation
The rotary evaporator enables the removal of solvent in a controlled manner under vacuum. Reducing the pressure in the rotary evaporator by a vacuum pump lowers the boiling point of the solvent to be removed; specifically ethanol in the case of cannabis extract processing.
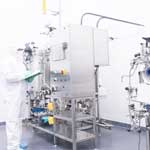
Falling Film Evaporation
Large volumes of cannabis ethanol extract can be concentrated utilizing a falling film evaporator. LNEYA provides a variety of styles of refrigeration and heating circulators to promote ethanol evaporation and coolers to condense ethanol vapor.
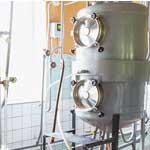
Vacuum Distillation Cooling
Isolation of high purity THC or CBD for medicinal and recreational applications requires additional processing.
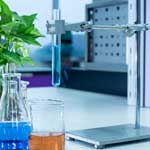
Short-Path Distillation
The condenser is cooled with a recirculating chiller to provide cooling for condensation of the component vapors. As the vapor temperature increases, indicating a new compound/mixture fraction, the multi-position receiving flask is adjusted to isolate the different fractions of terpenes, THC, and CBD.
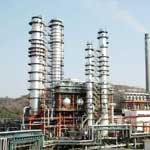
Fractionating Column
To improve results over the short path method, a longer fractionating column can be installed between the vessel with heated oil and the condenser apparatus.
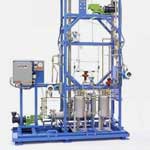
Wiped Film Distillation
A long, slender condenser in the middle of the apparatus, cooled with recirculating fluid, condenses the vapor.
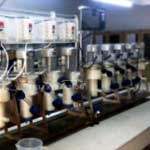
Liquefied Hydrocarbons
Recirculating temperature control units (TCUs) that can provide cooling to -60°C (-76°F) and below facilitates this process.
Products & Solutions
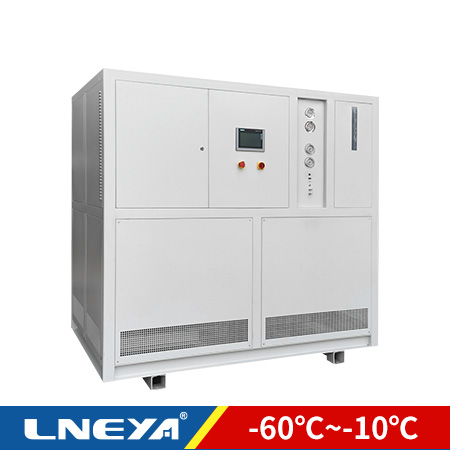
LNEYA LN series ultra-low temperature chiller, temperature control range -60℃ to -10℃, rapid temperature rise and fall of liquid, supporting cannabis extraction production and use.
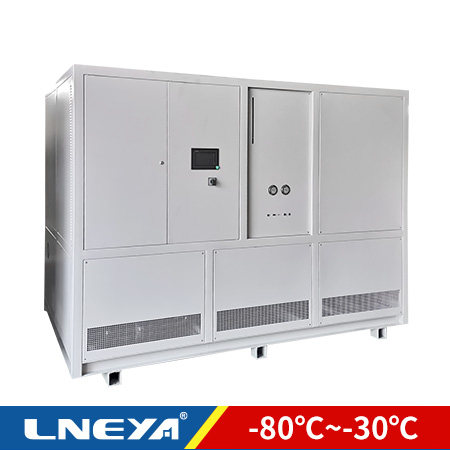
LNEYA LD series ultra-low temperature chiller, temperature control range -80℃ to -30℃, rapid temperature rise and fall of liquid, supporting cannabis extraction production and use.
Extraction Process Temperature Control Considerations
Current extraction processes include CO2, butane or propane, and ethanol. In each method, the extractant is cooled to a temperature that can reach -80°C (-176°F) and then compressed until it is liquefied. The temperature can be reduced by using a cooler. The cooler can be a standard device or a customized unit designed to meet the requirements of a unique temperature profile.
In commercial systems, extraction is usually carried out in a jacketed vessel. Water, oil or other liquids circulate in the jacket through a temperature control unit (TCU), which can maintain a consistent temperature of the container wall and the extraction chamber.
Temperature control must be carried out in all steps of the process, but precise temperature control of the extraction chamber is absolutely critical to managing the quality and characteristics of the final product. This high level of control must also be reproducible from one batch to another, and must actually be performed continuously on a large number of batches. Controlling the temperature within .275°C (.5°F) is a standard that allows the finished product to be consistent. It is also important to note that in addition to accuracy, repeatability is extremely important for producers because it allows producers to replicate the process over time, thereby ensuring consistent product quality.
For example, Increasing the extraction temperature from the initial reagent temperature:
• Reduce the concentration of terpenoids in the extract
• May denature the final CBD/THC product
• Increase the extraction volume and total volume of wax/resin, but the yield is lower
Similarly, lowering the extraction temperature will lead to:
• Increase the concentration of oil in the extract
• Reduce the proportion of wax in the extract
For these reasons, it is very important for producers to have equipment that can perform consistent and accurate temperature control; and, because of the need to make many changes to the final product of the extraction process, there are high-precision cooling equipment and temperature control units. , Closed-loop control is essential.
After the extraction process is complete, the processor will leave 55-75% of the cannabinoid “crude extract”, and in some cases can be sold without further processing. However, for most processors, the remaining elements must be further separated to obtain fully purified high-value CBD/THC oil.
The next step in the purification process is to cool the extract to approximately -20°C (-4°F) in a jacketed vessel driven by a cooler to remove the wax. This “winterization” process precipitates some unwanted elements from the solution, these elements leave behind an oil composed of cannabinoids, chlorophyll and terpenes after filtration. Decarboxylation is an important step that can be performed before or after the winter process. It is used to activate the CBD/THC component and can be done by carefully heating the extract to release the carboxyl group (COOH).
Distillation process-temperature control considerations
Then a distillation process is carried out to complete the separation of the remaining elements and produce the purest CBD or THC oil. It is worth mentioning that even if the raw materials have undergone antifreeze treatment, as many as 40% of the remaining raw materials may be composed of undesirable materials. Likewise, in the case of ethanol extraction, the ethanol must be evaporated to separate it from the CBD/THC components.
Like the extraction process, the distillation process for the complete purification of CBD/THC oil requires strict control of temperature, pressure, and feed rate of raw materials to ensure that the necessary interactions produce high-quality finished products with the highest possible characteristics. value.
The most common equipment is wiping film, molecular short-range still images. In this method, although the typical distillation temperature range is 130-180°C (usually 130-180°C (266-356°F)). In these systems, the raw materials are distributed in the evaporation chamber by special wipers On the wall. The film produced allows the more volatile terpenes to evaporate through the top of the reaction chamber into its own external collection container, while the CBD/THC is collected along the central condenser unit controlled by the TCU, which has a lower temperature ( Usually 60-70°C/140-158°F) is higher than the evaporation chamber and can attract cannabis vapor. The last step of the process is to remove the solvent, which is done separately.
Some original equipment manufacturers provide wiped-film molecular short-path distillation equipment that directly integrates the removal of heavier materials into their distillation process. In this case, chlorophyll, wax and other heavier residues (up to 40% of the feed) fall from the outer wall of the distillation vessel and collect in the designated container.
In some cases, a final separation step will be taken to separate THC from CBD. Crystallization is a common method. Fill the reaction vessel with raw materials and solvent, and slowly cool it from 60°C to -20°C. A slurry is formed, which is then transferred to a Nutsche filter dryer to produce pure dry crystals. The Nutsche filter is a jacketed container whose temperature is controlled by a circulating hot oil device. This method can produce CBD or THC products with a purity of 98% or higher.